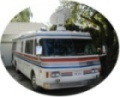 Expert
   Location: Cottage Grove, OR | The following writeup was done by Lou Cruse and is posted here with his permission. The pictures he references will be posted to the Album section. Timbren Rubber Spring Install 8-23-10
RVS sells the kit (pictured) for $270 +shpping (in 2008). It includes the A103B-65 donut rated at 3,500 lbs. That kit is what I put on #120, as shown in the pictures. If you make your own plates they can be any size that matches the end of the donut. They can be round, rectangular, other, but must clear the shock and the tire as the suspension arm swings thru its arc. The RVS plates are 1/4" thick. The donut expands in diameter as it gets loaded so adequate clearance in that "squished" condition is required. The "installed" ideal is where the donut is sitting straight up and down, squished slightly, and between the stock upper plate and the plate welded on the suspension arm, and those plates are parallel when the vehicle is sitting on the tires with its regular load on the suspension. The "raiser" on the small end of the plate does not have to be used IF you make a wedge type plate, but think how you are going to weld it to the arm. Thick and thin sections require different heat input. Crawl under a get a measurement of the distance between the top of the suspension arm at the bottom of the sheet metal rectangular bumper support. Write that measurement down. Remove the rear tires for installing the donuts. Let the suspension come all the way down, the shock full extension will stop it. Remove the stock rectangular "bumper". I used an existing bolt hole (drilled out bigger for 3/4"-16) bolt used in DoNut) for the donut mount. NOTE: If you use the enlarged "stock" bolt hole, the donut may hit the inside tire when it gets squished out. Mine did. I discovered this after I got EVERYTHING done ! I went back and moved the bolt hole in toward the center line of the frame 1/2 inch. The plate still clears the shock by about 3/4" and the donut just clears the tire. Getting an enlarged hole moved in 1/2" is tricky, and may require grinding. Think how you are going to gets this new 3/4" hole moved in 1/2" before you start and "lose" the original stock bolt position. I guess some slight outer diameter trimming could be done to the donut to clear the tire but it should not be much. How much ? I have no idea. You have to weld on the small flat bracket that has a little "raiser" welded on the small end. Get a longer bolt to stick down to position the plate on the suspension arm. Jack the arm back up into the Torsion Bar stock (where it sits with the tire on) height duplicating the measurement you made when you crawled under it. With the "alignment bolt in ther center of the plate, clamp the plate in that position. You might have to let it down some to get the clamp on. Tack weld the plate to the arm. Jack the arm back up and convince yourself that the plate is in the right position to support the end of the donut as the suspension arm moves up and down in its arc of travel. If suitably positioned, lower the arm to give you some more room. Weld the plate to the arm. That arm is very STOUT . . . do not worry about distorting it during welding. Use enough welding juice to get good penetration in the arm and the plate without melting the plate away. I used regular 6013 arc welding sticks, with about 90 amps on a AC type 225 amp Arc Welder. Crawled around a lot to get in position but could use about half a rod as continuous welding before I would pull it and examine the weld. Moved around to weld one end then the other, inside then outside. A wire welder would, of course, be easier. Maybe a little Rustoleum type paint after cleaning up the welds. Next, install the donut. You can see in the RVS Kit picture where they grind/cut a little of the top of the donut to clear the frame support bracket. Put the bolt and washer into the donut then put the bolt up thru the enlarged hole, then a washer and self locking nut. You might have to put a long screw driver on the head of the bolt to help push it up thru the chassis plate hole. It is hard, but you can push an open end wrench up inside the donut to hold the bolt head while you tighten the exposed nut. Get the nut tight, but dont distort the donut more than just a little. I used a Ny-Loc nut, but I guess a lockwasher could be used as nothing is hot around the nut so the lock washer should act like a lock washer for a long time. I just don't use lock washers. There are 3 additional pictures of the RVS installation of their suspension kit on FMC #622. The work was done at RVS Morgan Hill, but I took those pictures when it lived here in Aridzona. Note that the "raiser" is a little higher than the ones that came in my RVS Kit. The "raiser" seems to be several small plates welded together. This indicates that there will probably be some variation in the actual position of the bolt hole in the chassis "bumper" bracket from coach to coach. Such variation is common in welded assemblies. I recommend using to the Timbren A103B-75 donut rated at 4,000 lbs. Both donuts are the exact same size. The higher rated one uses a 75 Shore durometer rubber instead 65, which makes it a little "stiffer". If I ever replace the ones on #120 I'll use the higher rated A103B-75s and get them direct from a Timbren dealer here in Phoenix (there are 3 Timbren dealers here in AZ). You can buy the donut(s) direct from Timbren or a dealer. A pair of A103B-75 Timbren Donuts will cost me $120 here in Phoenix at full Retail Price. http://www.timbren.com/aeon-single-convolution-springs.htm The Timbren "factory" is in Whitby, Ontario (800) 263-3113 Perhaps this brief writeup and pictures will be useful if you install the Timbren Rubber Springs to your FMC rear suspension. You are encouraged to forward, copy, post, share, slice, dice, bend, staple, etc. in any way that may be helpful to any FMCer. Press On, Lou #120
|